CLEANING OUR AIR
TM SYSTEMS HELPS INDUSTRIES TO TACKLE GLOBAL EMISSION PROBLEMS
Our patented, award-winning emission control system, Zero-Ex®, is a versatile and cost-effective technology designed to reduce emissions, eliminate airborne pollutants, control odors, and capture particulate matter.
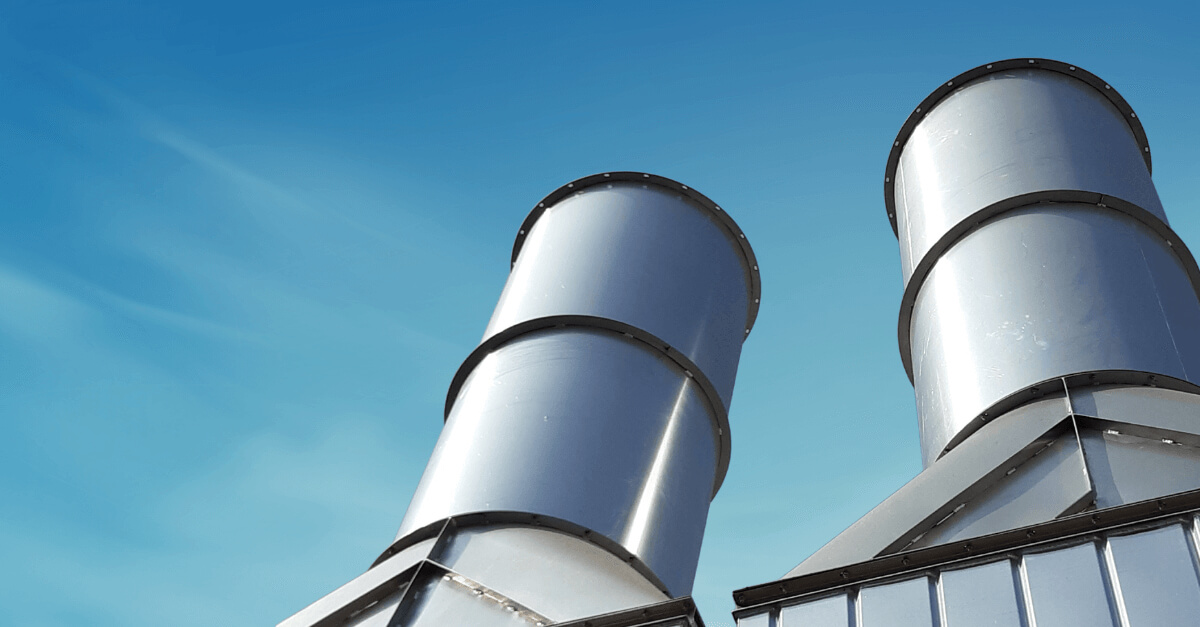
ZERO-EX® – AWARD-WINNING EMISSION CAPTURE TECHNOLOGY FOR PROCESS AND MANUFACTURING INDUSTRIES
If you’re looking for an effective solution to eliminate harmful pollutants and odors from your process exhaust streams before they pollute the atmosphere, consider the power of Zero-Ex® emission reduction technology.
Zero-Ex is a versatile and cost-effective pollution control technology capable of eliminating over 99% of airborne emissions, odor and particulate matter.
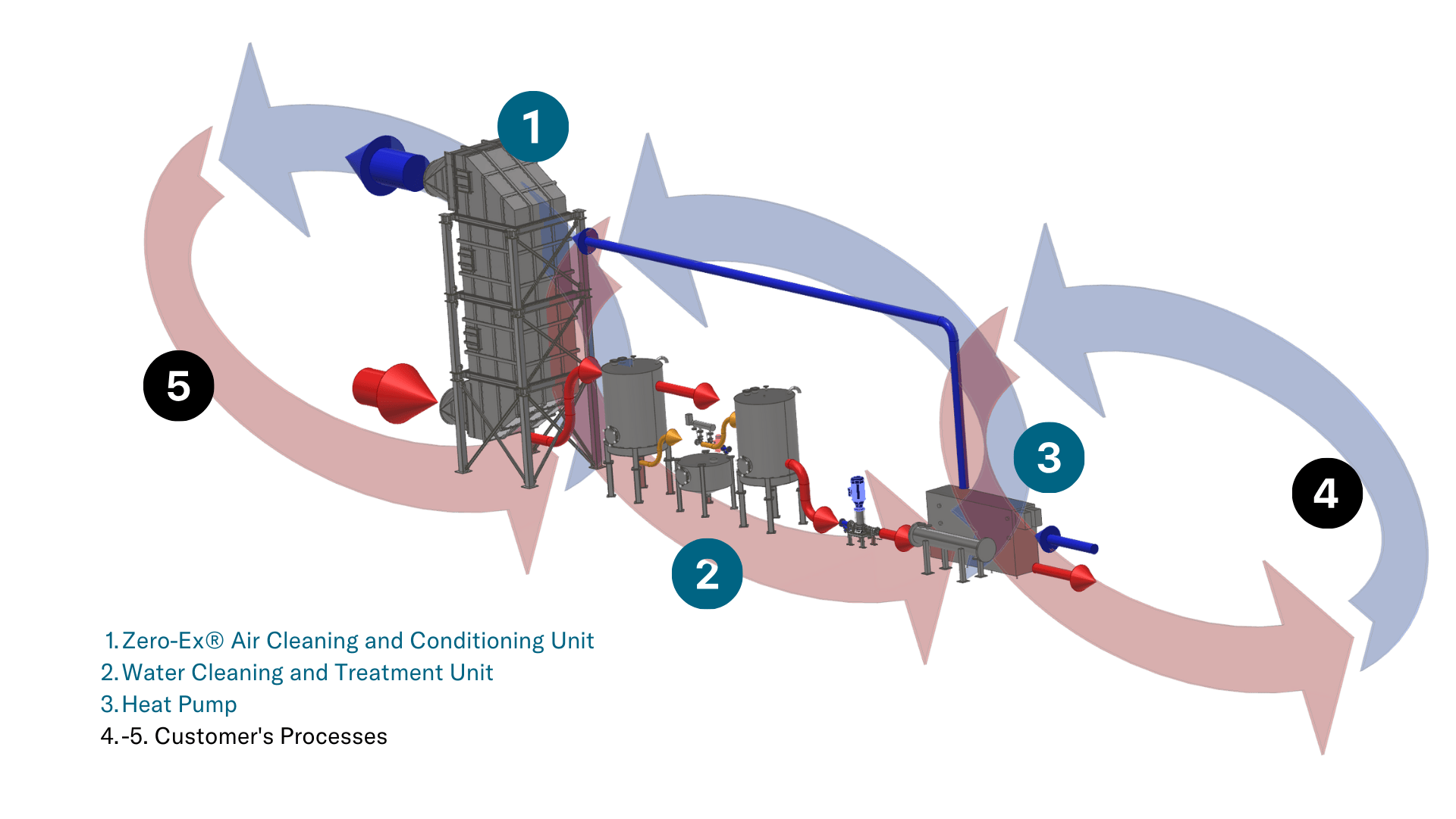
HOW DOES IT WORK?
The general layout of the Zero-Ex® emission control system includes an air cleaning and conditioning unit, water cleaning and treatment unit, and a heat pump. For gaseous emissions, such as VOCs, particle separation is either combined with or replaced by a chemical treatment unit. Waste heat from both sides of the process can be fully recirculated within the customer’s processes.
For example, the customer can utilize all excess heat and energy in its own processes, such as hot water (100°C) for process heating, HVAC, or chilled water at 7°C for process cooling and HVAC.
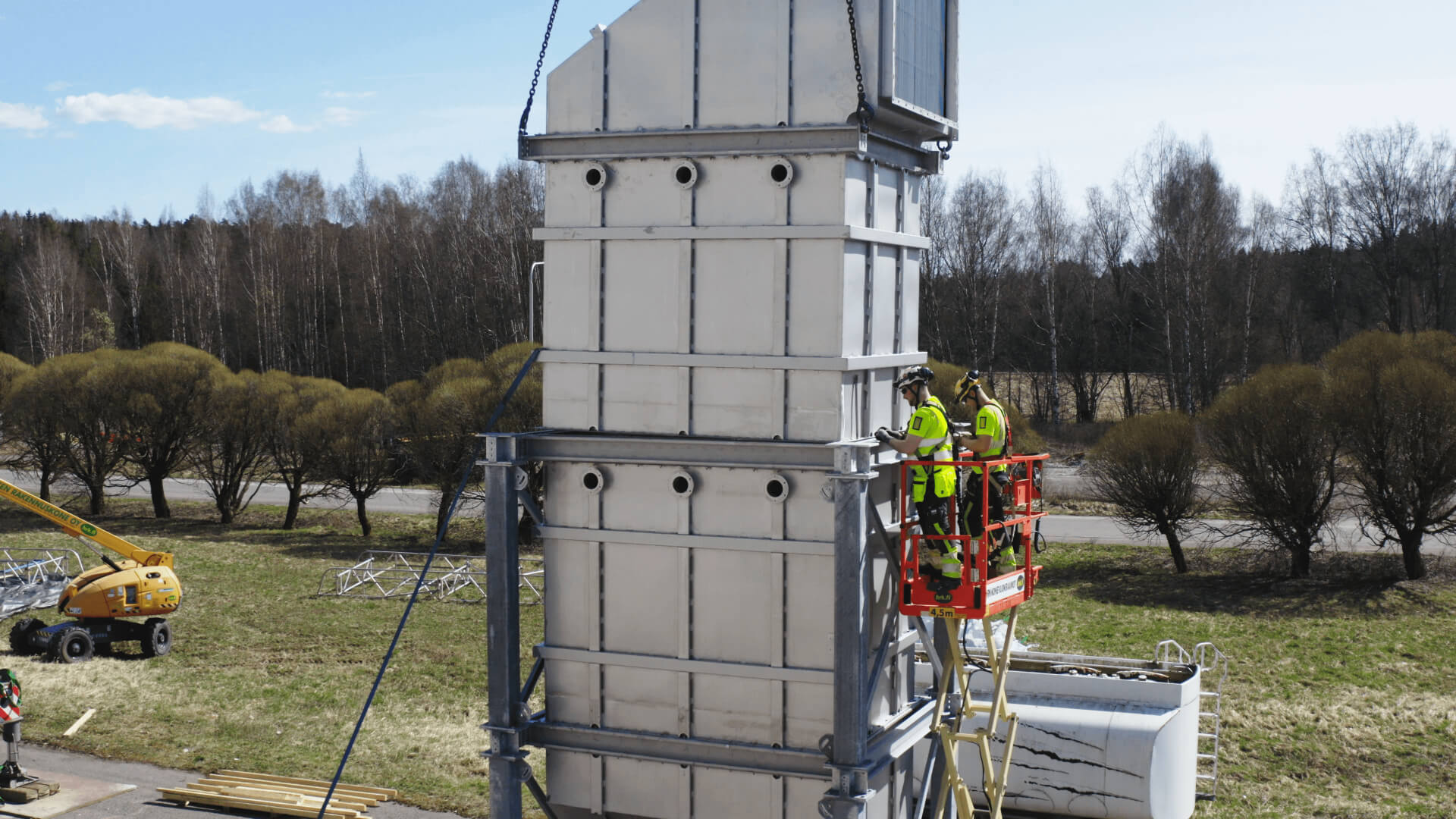
ZERO-EX IS A CLOSED-LOOP EMISSION CONTROL TECHNOLOGY
Zero-Ex is designed to capture industrial emissions and visible vapors, promoting sustainable production across various processing and manufacturing industries including mechanical forest industry, pulp and paper mills, food processing plants and packaging industry.
KEY BENEFITS
Zero emissions: Efficient purification and elimination of emissions, VOCs and odor, GHGs and PM, fog, noise and dust.
Energy & water savings: Significant savings, especially for pulp and paper mills, can be achieved through our advanced scrubbing system.
This innovative solution allows for the recirculation of water, while energy is efficiently transferred to the water medium and subsequently to other locations via a heat pump. This method maximizes energy efficiency by reducing reliance on fans, heat pumps, and water pumps, while it also minimizes water usage, resulting in substantial overall resource savings.
CLOSED RECIRCULATION AND LOW ENERGY CONSUMPTION
- Versatile & retrofittable: Suitable for any exhaust quantity and can be integrated into existing processes.
- Closed recirculation: Process air and water can be recirculated back.
- Technical features: Low energy consumption, efficient heat recovery, low noise levels, scalable.
- Economic benefits: Energy efficiency and low OPEX and service costs.
EXCELLENT NORDIC AND ASIAN REFERENCES (FOOD, FOREST, AND PAPER INDUSTRIES)
- Over 90% reduction of VOCs (in response to local environmental agency complaints).
- 98% sulfur compounds were reduced.
- Fog, dust and noise decreased significantly (close to zero).
Want to learn more? Watch how Zero-Ex is integrated into SuperDryer™ for maximum benefit!
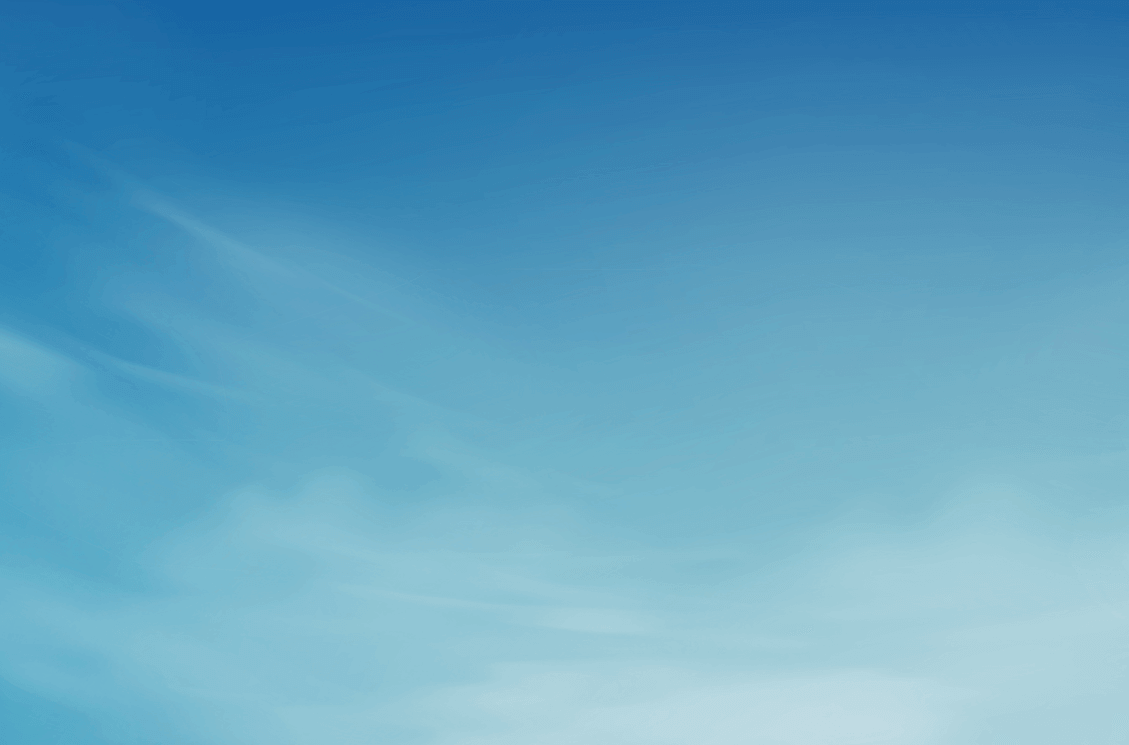
LATEST ZERO-EX DELIVERIES
Delivery of SuperDryer™ to CH-Bioforce’s biomass processing plant in Finland. At the plant, food industry and agricultural waste is transformed into valuable raw materials for industries such as textiles, pharmaceuticals, and cosmetics.
Heat recovery and emission control of turbo exhaust for an Asian paper manufacturer.
Five Zero-Ex units delivered to a long-term Chinese customer to remove fog and airborne emissions from the exhaust air.