PROCESS TECHNOLOGY BY TM SYSTEMS
PROCESS TECHNOLOGY BY TM SYSTEMS – REBUILDS, OPTIMIZATION AND NEW PRODUCTION PLANTS
TM Systems specializes in process optimization and decarbonization for the processing and manufacturing industries, helping customers achieve energy and production efficiency targets.
Our solutions include critical components for the pulp and paper industry, such as trim handling systems and runnability components. We also provide process technology that is suitable for industries like food, forest, mining, and energy, with specific goals for energy efficiency and noise control.
HOOD TECHNOLOGY
PROCESS TECHNOLOGYDRYER SECTION AIR SYSTEMS
PROCESS TECHNOLOGYPOCKET VENTILATION
PROCESS TECHNOLOGYWEB STABILIZERS
PROCESS TECHNOLOGYWIRE SECTION VENTILATION
PROCESS TECHNOLOGYPULPER EXHAUST SYSTEMS
PROCESS TECHNOLOGYINDUSTRIAL NOISE CONTROL
PROCESS TECHNOLOGYTRIM HANDLING
PROCESS TECHNOLOGY
CONTACT OUR EXPERTS FOR MORE INFORMATION
Our experts are here for you. Leave us a message here or contact us directly:
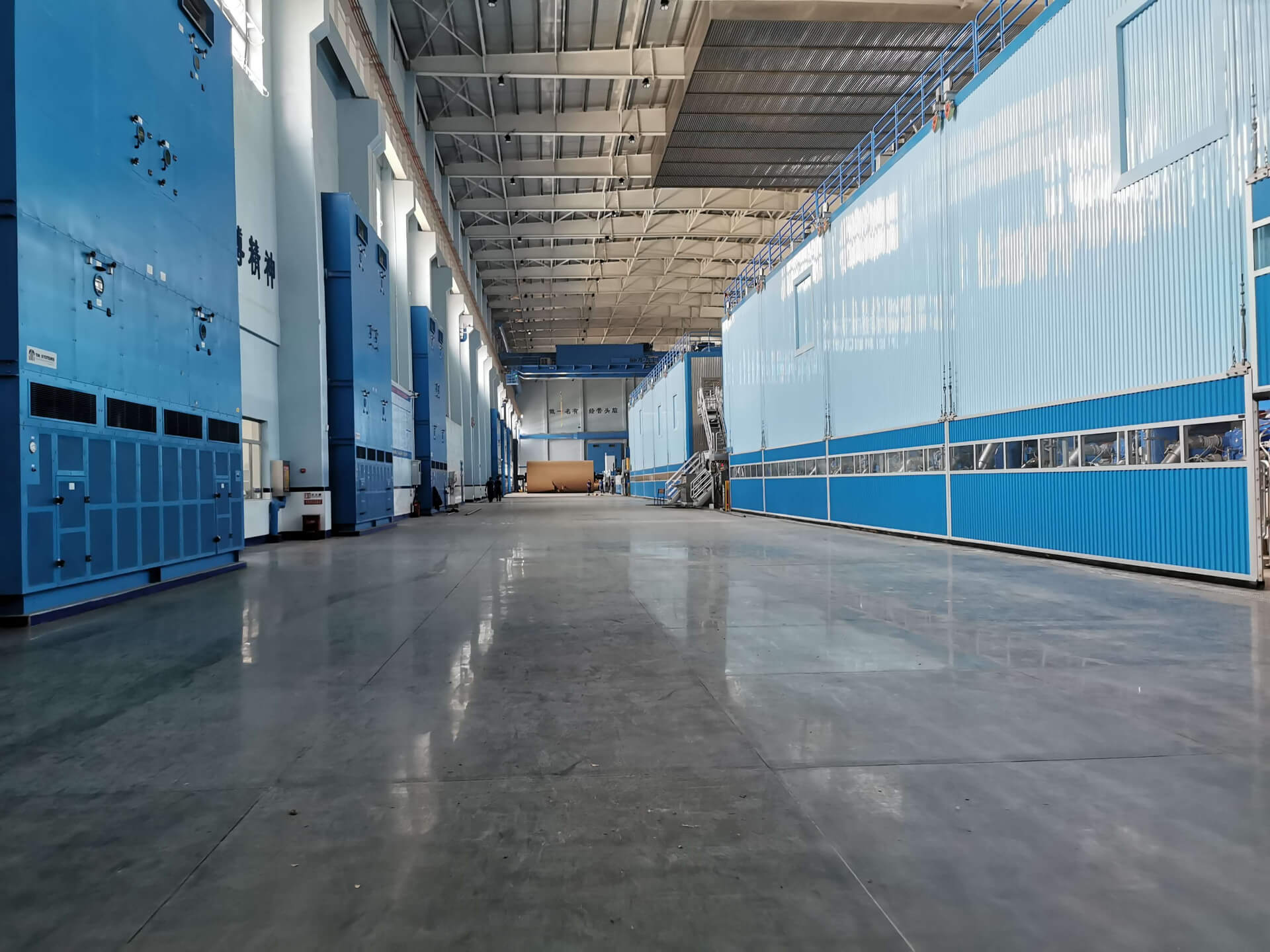
STATE-OF-THE-ART HOOD TECHNOLOGY
With over 50 years of experience, TM Systems has delivered high-quality hoods and hood rebuilds to a global customer base.
A high dewpoint closed dryer section hood is an essential part of a modern paper or board machine, but it can also greatly improve the dryer section efficiency of older paper machines.
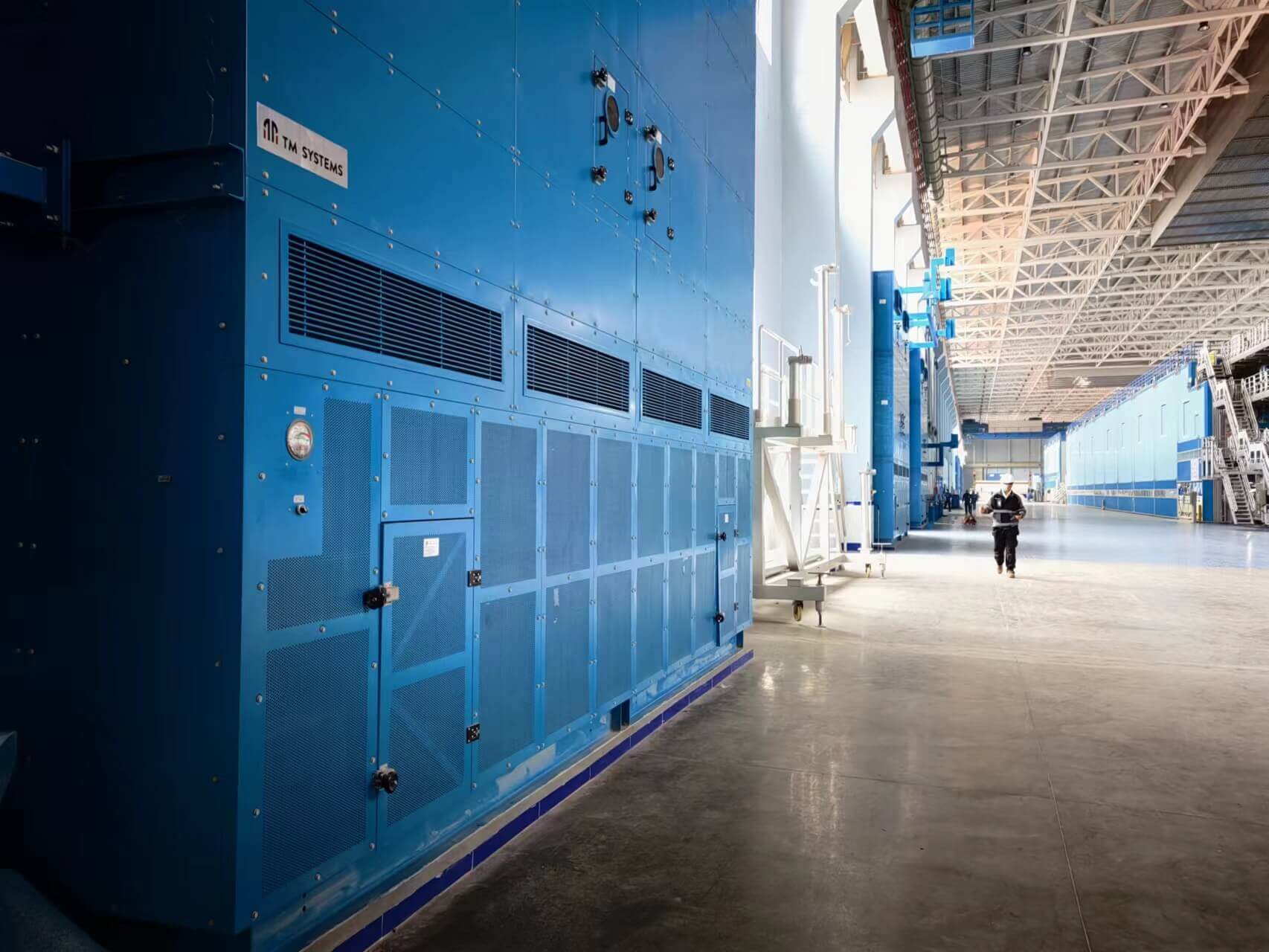
TM Systems offers modern solutions for closed high dewpoint hoods and open canopy hoods. For a turnkey solution, our hoods can also be offered with complete dryer section process ventilation, heat recovery, and runnability components.
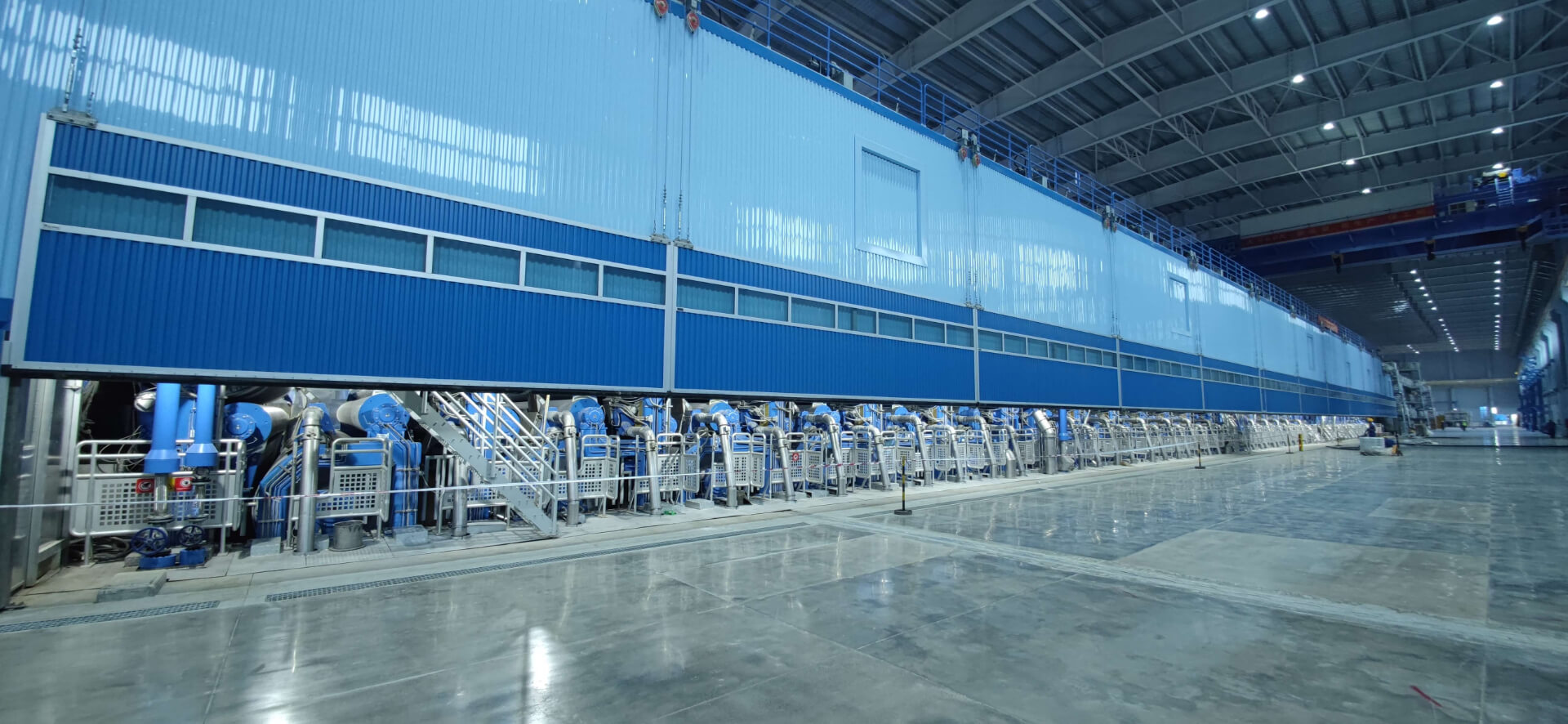
KEY BENEFITS
- Protects machine operators from noise, dust, heat radiation and humidity
- Provides even and optimal conditions for web drying
- Collects the energy used in web drying and prevents heat and humidity from spreading into the machine hall
- Minimizes energy costs
- Maximizes the potential for heat recovery
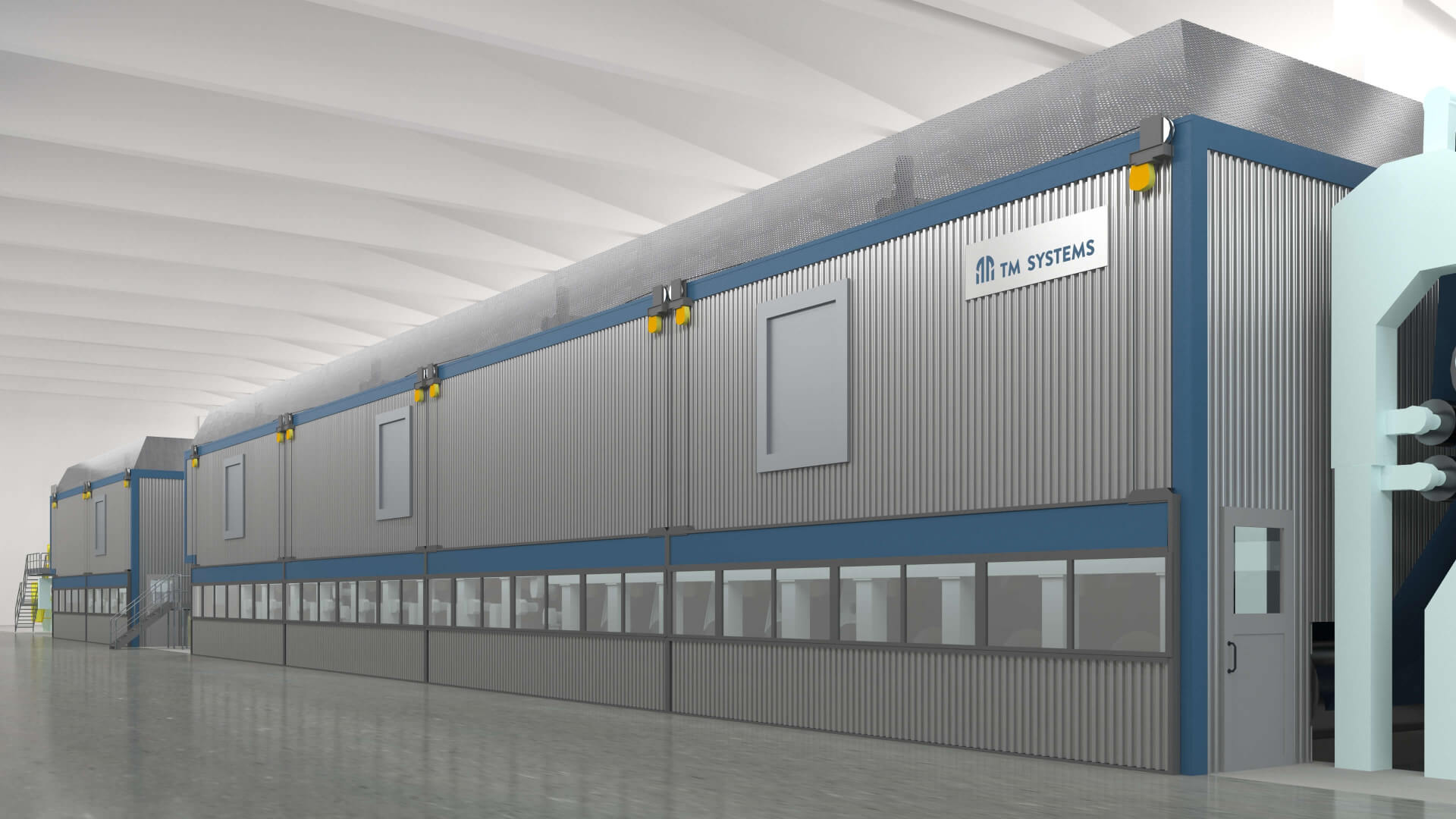
LATEST REFERENCES
A successful delivery of a complete hood and air systems to a Swedish customer.
TM Systems successfully completes a large project delivery: hood, air system, wet-end process ventilation, runnability components, heat recovery, and hall ventilation delivered to the world’s leading pulp and paper manufacturer.
Hood and air systems project completed for a packaging company in Indonesia.
TM Systems delivers hoods, dryer section air systems, heat recovery, pulper exhaust systems, and a comprehensive machine hall ventilation system to the world’s leading paper manufacturer.
DRYER SECTION AIR SYSTEMS – INCREASED PAPER QUALITY, PRODUCTIVITY AND RUNNABILITY
Dryer section air systems consist of key components that affect paper quality, productivity, and paper machine runnability.
With extensive experience in the field, TM Systems can supply all necessary components to ventilate the dryer section: exhaust air systems, supply air systems, pocket ventilators and other dryer section air distribution devices.
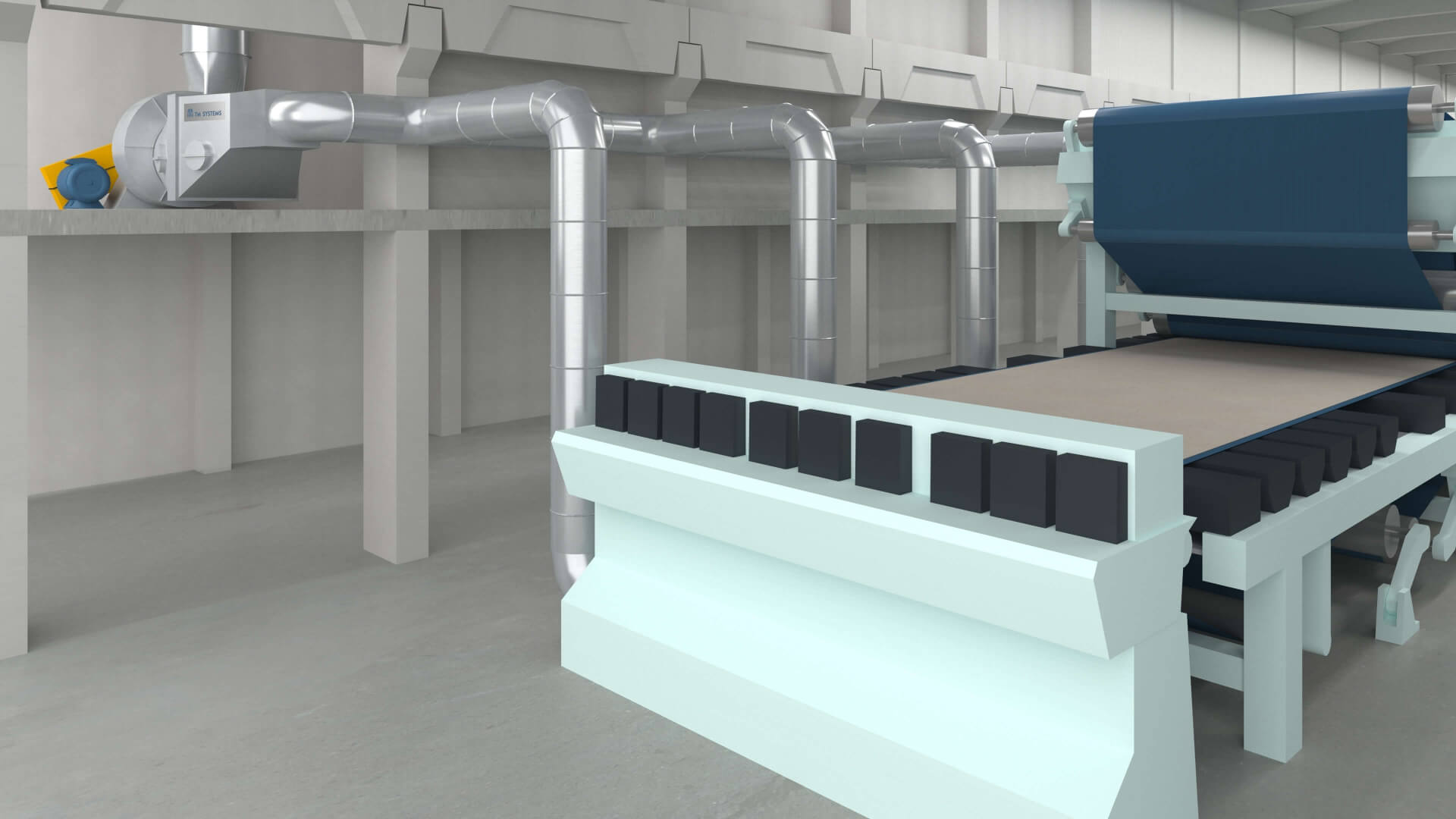
KEY BENEFITS
- Even ventilation throughout the hood
- Sustainable moisture levels for efficient drying and heat recovery
- Improved machine speeds and production rates
- A stable web with the assistance of our runnability components
ENERGY EFFICIENT POCKET VENTILATORS
Our ventilation systems are designed to efficiently supply and exhaust air to and from the drying section, allowing for an efficient and controlled drying process. The evacuated moisture and heat are then recovered in our heat-recovery systems to minimize energy costs for running the process.
The Moist-Ex® ventilation unit is a modern and improved alternative to standard pocket ventilators, based on both blowing and suction ventilation.
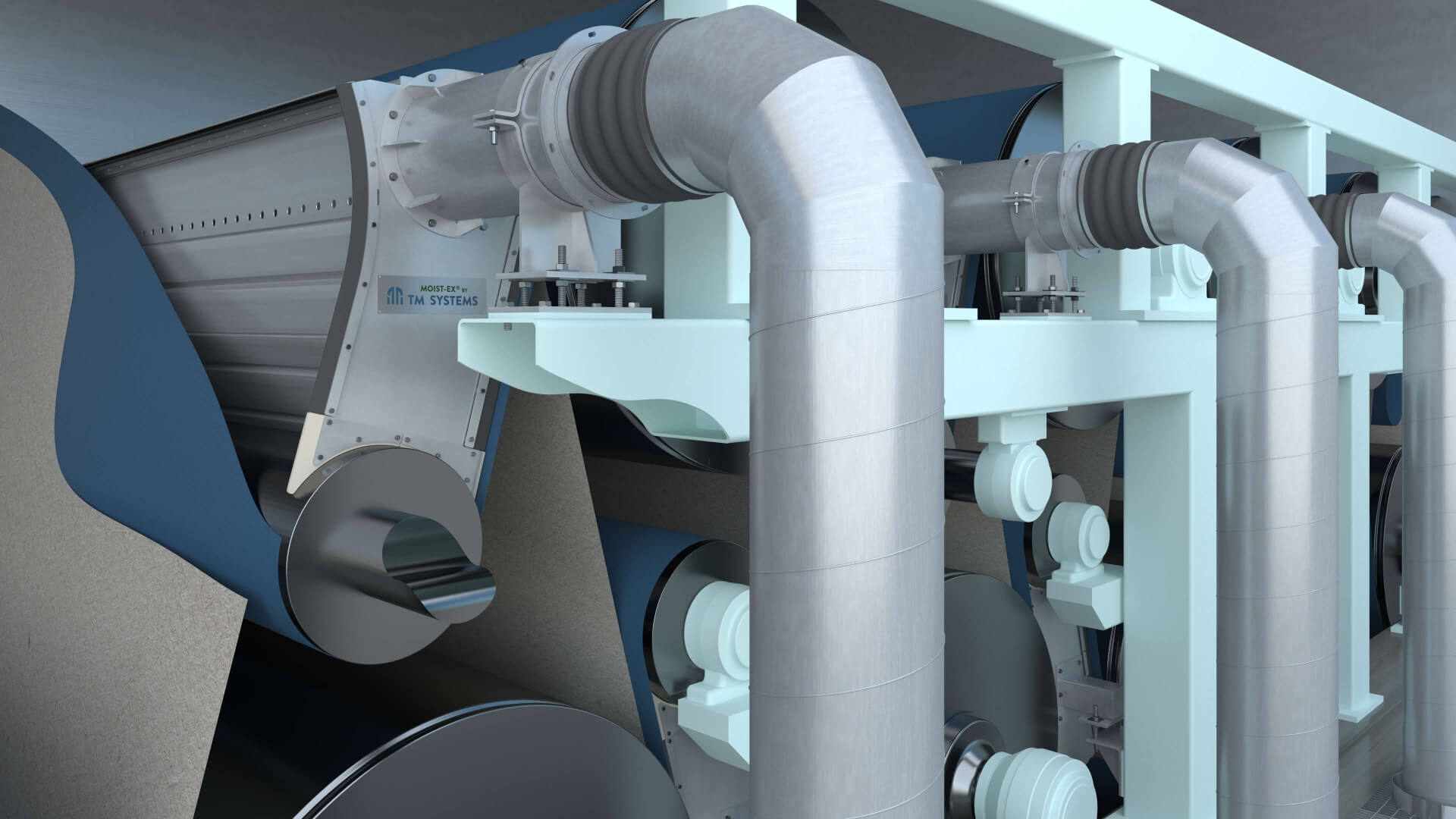
HOW CAN I BENEFIT?
The major benefits of Moist-Ex pocket ventilation include the ability to allow an even higher rate of evaporation from the paper web, enabling increased machine speeds and production. The higher moisture in the exhaust air also increase production and efficiency of the heat-recovery system.
TM Systems’ runnability components ensure that the paper web runs cleanly throughout the machine without risks of web breaks, tears, or folds that can create uneven edges on the end-product.
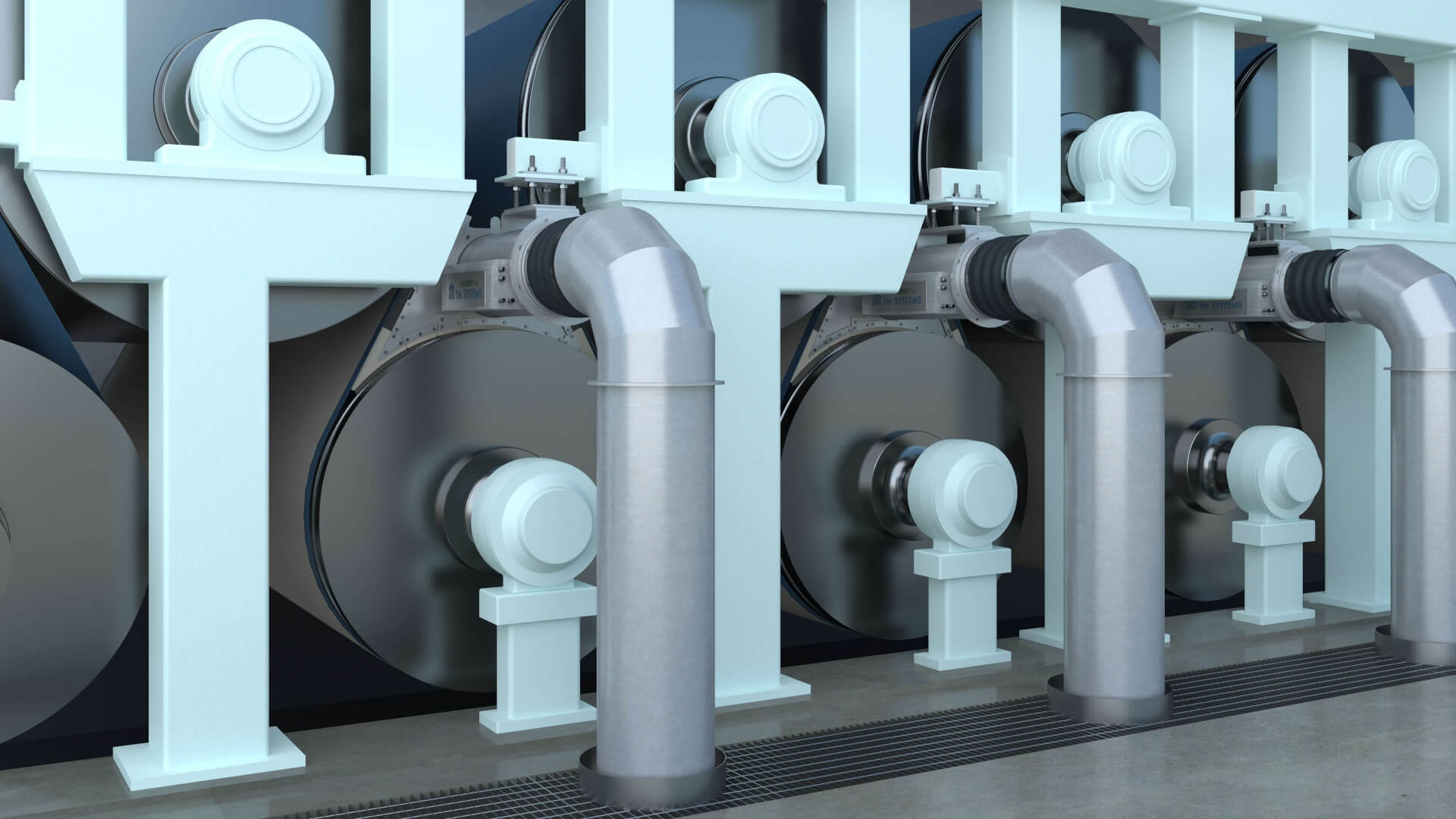
ENERGY SAVING WEB STABILIZERS – VACUBOX®
Vacubox® web stabilizers and pocket ventilators increase production and the efficiency of the paper machine while also improving runnability and paper quality.
TM Systems offers Vacubox X web stabilizers for press sections, Vacubox P transfer boxes, Vacubox S and 2S single or double-sided web stabilizers for slalom sections, and Vacubox 3S web stabilizers for use in slalom sections with suction rolls. Also, High Vacuum HV-variants with an integrated release zone and versions with tail threading support zones are available.
WIRE SECTION VENTILATION AND PULPER EXHAUST SYSTEMS
EFFECTIVE REDUCTION OF MOISTURE LOAD
TM Systems provides wire section ventilation systems and pulper exhaust systems to ensure that heat and humidity do not spread from the wire section. We have delivered both new solutions to our customers and also assisted them when they upgrade their machines, for example, by expanding the wire section.
When production increases, the heat and humidity load also rises. Increasing the pulp volume generates more heat, and we at TM Systems are here to help with that.
Our equipment improves the working environment and enhances the performance of surrounding machinery.
INDUSTRIAL NOISE CONTROL
NOISE CONTROL SYSTEMS – WIDE VARIETY OF SOLUTIONS FOR NOISE ATTENUATION
As environmental permit requirements tighten, the criteria for noise pollution, among other things, are also becoming stricter.
Why TM Systems? We have provided different noise control solutions for decades. Nearly every one of our projects has included noise attenuation, and due to increasingly stringent regulations, we are now improving our customers’ existing noise reduction solutions.
CHECK OUT OUR LATEST PROJECTS
Delivery of heat recovery tower and machine hall ventilation system for a customer in the Finnish packaging industry.
A successful delivery of a complete hood and air systems to a Swedish customer.
TM Systems successfully completes a large project delivery: hood, air system, wet-end process ventilation, runnability components, heat recovery, and hall ventilation delivered to the world’s leading pulp and paper manufacturer.
Delivery of SuperDryer™ to CH-Bioforce’s biomass processing plant in Finland. At the plant, food industry and agricultural waste is transformed into valuable raw materials for industries such as textiles, pharmaceuticals, and cosmetics.
Trimvac survey and troubleshooting for an Austrian customer.