TM Systems has delivered SuperDryer™ technology to CH-Bioforce‘s biomass processing plant, where agricultural and food industry residues are converted into valuable products for industries such as textiles and cosmetics.
The project began in 2022 when TM Systems received significant EIC funding from the EU for the full-scale commercial launch of its ongoing product development project, SuperDryer. By September 2024, the installation process for the first customer was completed, allowing the commissioning phase to begin at the customer’s biomass processing plant in Southwest Finland.
TM Systems has made tests of the drying line using various biomasses and products, including those from third parties. The commissioning phase and ramp-up of the drying line took place in fall 2024, with a final annual production capacity of 15,000 tons.
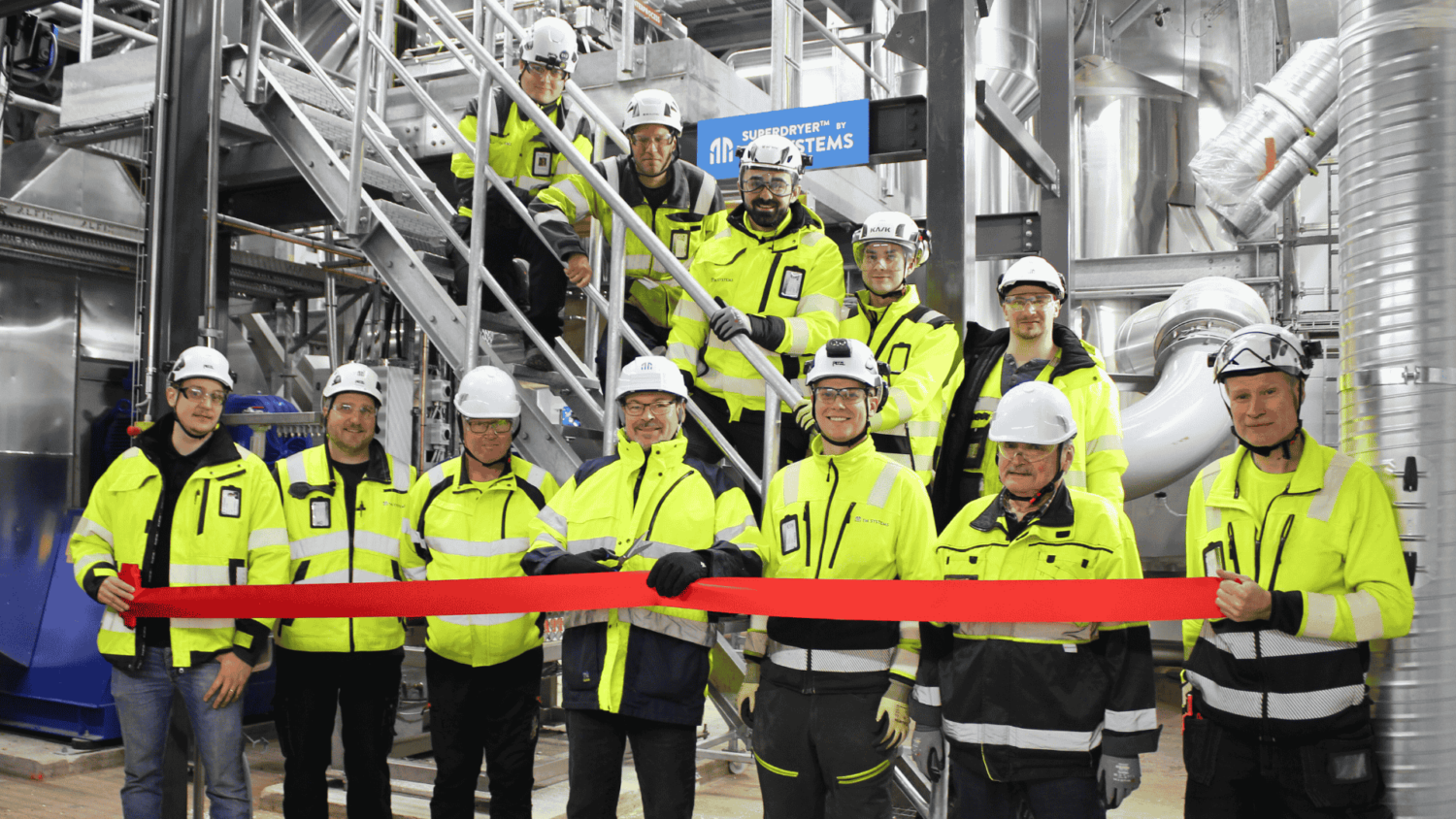
Picture: The team behind the project! This picture was taken at the ribbon-cutting ceremony organized by TM Systems.
INNOVATIVE PRODUCT DEVELOPMENT LEADS TO A CIRCULAR SOLUTION
The world and business environments are changing, pushing companies to utilize their side streams more resourcefully. Due to biodiversity loss, there is a growing need for more resource-efficient approaches, including circular economy solutions that optimize biomass use. In response to this need, TM Systems is developing drying technologies that add value to biomass through drying.
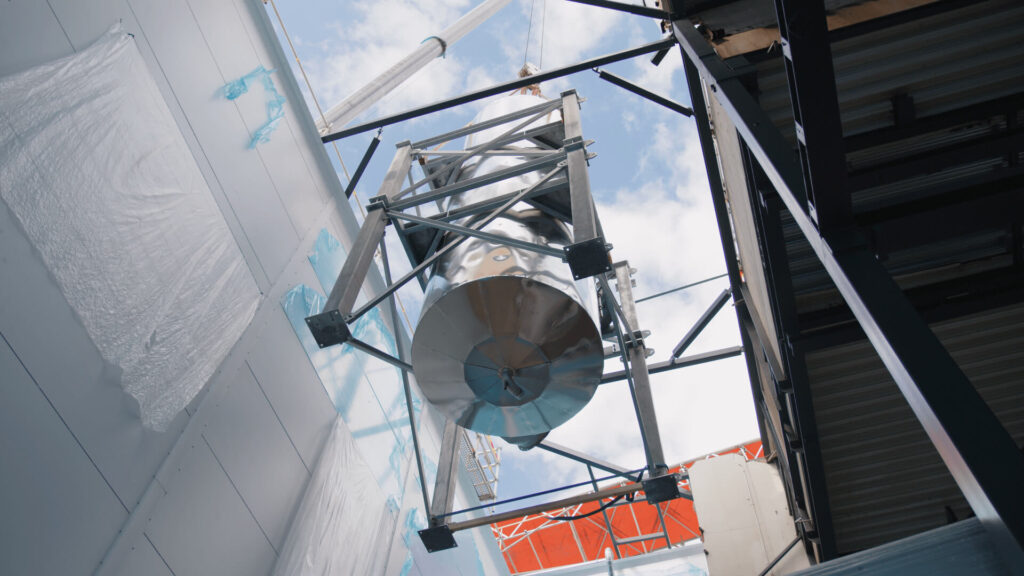
Picture: SuperDryer’s retrofit characteristics allow it to be installed in existing processes or limited spaces.
In 2022, TM Systems advanced its technology by developing an emission-free dryer based on combined expertise in air, energy, and materials. The new drying technology, SuperDryer, addresses critical industrial waste stream challenges, such as energy consumption and maintaining end-product quality. This development was supported by highly competitive EIC funding, with only 2–5% of applicants being awarded funding. The grant highlights the forerunner status of the technology and SuperDryer as an innovation.
SuperDryer is designed to meet stringent production and sustainability requirements. Its energy efficiency makes it the optimal choice for the customer’s production process. The dryer uses existing energy sources, such as steam, while the preheating coils in the air intake unit utilize waste heat from surrounding processes, significantly reducing energy demand and enhancing sustainability. The system allows for easy control of optimal drying conditions and final dryness with just a few operating parameters.
SuperDryer’s integrated Zero-Ex® technology recovers the latent heat from the evaporated water and efficiently cleans the drying air, minimizing dust and particle emissions.
SUPERDRYER’S VERSATILE APPLICATIONS
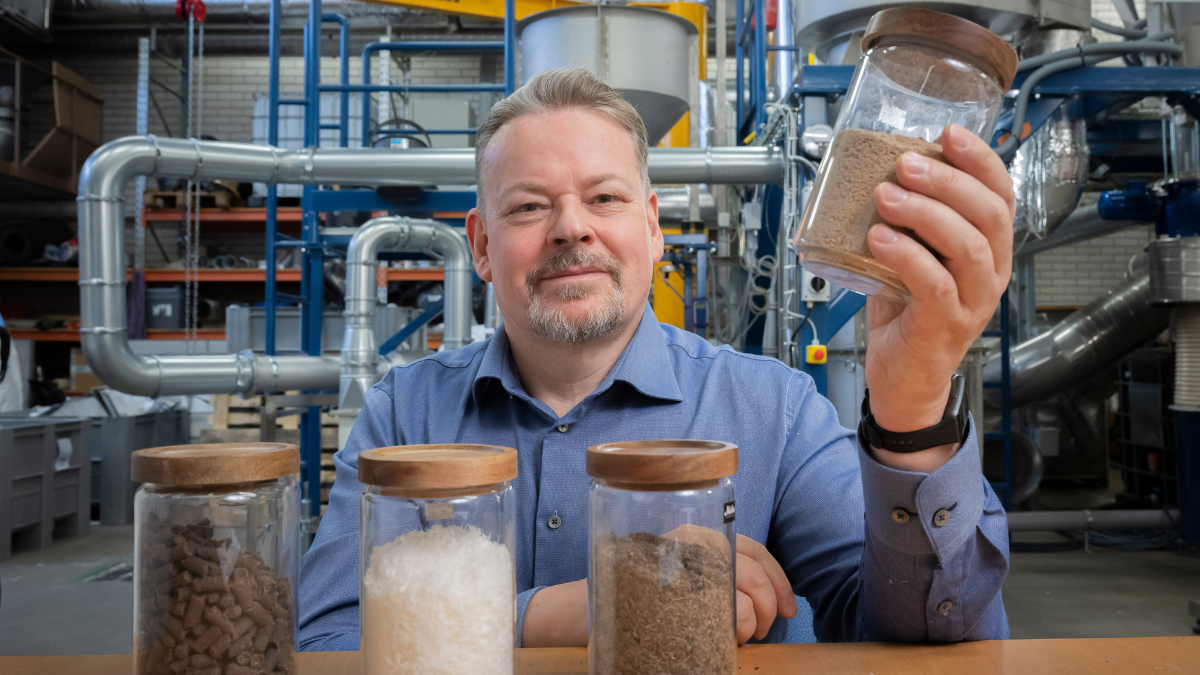
Picture: Markus Hallapuro, CEO of TM Systems, showcasing successfully dried biomasses from various industries.
SuperDryer is an optimal solution for drying a wide range of biomasses. It can produce bio-pellets with high energy content and recycled fibers that can be used as raw materials in multiple industries. The technology also enables biomass valorization, the creation of higher value-added biobased solutions, and the production of fertilizers and soil conditioners.
SuperDryer’s adaptability and scalability allows it to be installed in existing processes or limited spaces, as was done in this project. It can also be installed in new spaces, as well as retrofitted into processes when they are modernized.
Multiple test drying processes are currently underway at our research facility, and we welcome all interested companies to test dry their biomass and explore turning it into industrial installations. Contact our team to discuss further!
Aleksi Hidén
SuperDryer™ Specialist, TM Systems
firstname.lastname@tmsystems.com
Markus Hallapuro
CEO, TM Systems
firstname.lastname@tmsystems.com
Pictures: Valote Oy and Teknologiateollisuus